Rock Cutting for Flintknappers 101
The following article is a collaborative effort by various members of the Puget Sound Knappers. This 'How-To' article is in response to the many, many requests by flintknappers for information on how to cut slabs for flintknapping purposes.
Significant contributions from Jim Keffer, Jim Miller, Harvey Hughett and Rich Russell have help make this possible.
The Puget Sound Knappers welcome input from other PSK members as well as member of the larger community of knappers and rock hounds as well.
Please send input to the PSK webmaster @ 
The purpose of this “How-To’ article is to provide an introduction to cutting conchoidal (knappable) rock for the subsequent use in flintknapping.
Why cut rock for flintknapping? The primary reason most flintknappers cut or ‘slab rock’ is to get the largest amount of usable pieces from a given rock. This is particularly true for rock that is rare or unique – which usually translates to expensive.
The alternative to cutting or slabbing rock is to spall the rock using some type of billet. With very few exceptions, even a novice rock cutter with a decent lapidary slab saw can get many more usable slabs that they could by spalling the rock with a billet. For example, an oblong rock 8” long and 4” in diameter could yield eight ½” slabs for knife blades or twenty-one 3/8” arrowhead slabs.
The second reason for cutting rock is that this is the first step in creating preforms or ground blanks for Flake Over Grind (FOG) work.
There are several types of slab saw but this article will only deal with the basics of setting them up for cutting slabs. While small trim saws can also be used to cut small slabs but this article is mainly intended for those contemplating using larger lapidary slab saws.
- Setting up the saw
- The blade
- Detailed information about diamond saw blades on the Web
- http://en.wikipedia.org/wiki/Diamond_blade
- http://www.ukam.com/diamond_blade_guide.htm
- Types of blades
- Continuous rim – requires lubrication, good for all knappable rock. The thicker continuous rim blades tend to bend/warp less but grind away a bit more rock. Most knappers tend towards continuous rim blades, available in different thicknesses.
- Segmented – may be used dry, usually for asphalt, concrete, building material, suitable for some knappable rock. This blade has a wider kerf (wastes more stone) but is strong.
- Other factors
Diamond Blades
|
Warping Risk
|
Cost
|
Thickness
|
Lubrication required
|
Type Materials
|
Sintered
|
|
|
|
|
|
Wholly sintered
|
High
|
Medium
|
Low-Medium
|
Usually
|
Hard stone
|
Silver brazed
|
Low
|
High
|
|
Always
|
Hard stone
|
Laser welded
|
Low
|
High
|
|
Usually
|
|
Vacuum brazed
|
|
|
|
|
|
Nickel electroplated
|
|
|
|
|
|
- Conditioning the blades
- New blade requires ‘conditioning to insure the best performance. To condition a blade make your first cut on material that is soft and abrasive – a common clay brick is ideal for this purpose. This will assure that the blade is properly broken in by bringing the rim into concentricity with the arbor and will open up the rim, increasing diamond protrusion.
- Blade maintenance – periodic conditioning (see above) helps prolong blade life. One method is to rotate the saw blade backwards for a couple of revolutions by hand while lightly touching the cutting edge of the blade with a medium-fine abrading stone. The abrading stone removes metal that may build up over the diamonds, and keeps fresh diamonds exposed on the cutting edge.
In radical situations: If, upon inspection with a magnifying glass, you discern “holes” in the blade edge where diamonds should be, and your saw is not cutting well, there’s a chance that your rock speed/feed pressure is set too high and you may ripping diamonds off the blade surface. In this case, you may want to make a few cuts through an old grinding wheel. If done carefully, you can wear away blade metal, exposing new diamonds. Periodic cutting a brick will help keep your blade sharp, particularly important when cutting hard rock. Running blades slower and cooler should help prevent diamond loss. Obsidian requires infrequent touching up of the blade. Hard rocks, such as agate or jasper, will require more careful use of your blade to avoid damage.
- Lubricants
- Purpose of lubricants
- Types of lubricants
- Water
- Vegetable oil
- Biodiesel
- Diesel, kerosene, Hydraulic fluid, etc.
- Mineral Oil/Commercial cutting oil
Product
|
Flammability
|
Rust Inhibit
|
Toxicity
|
Handling
|
Odor
|
Cleanup
|
Reclamation
|
Disposal
|
Lubricity
|
Cost
|
Water
|
low
|
none
|
low
|
good
|
good
|
easy
|
0
|
4
|
poor - fair
|
0
|
Kerosene
|
high
|
poor
|
medium
|
odor/contact
|
fragrant
|
difficult
|
tbd
|
7
|
fair
|
$9-$10/gal
|
Diesel
|
high
|
poor
|
medium
|
odor/contact
|
fragrant
|
difficult
|
tbd
|
7
|
fair
|
$4/gal
|
Vegetable Oil
|
medium
|
medium
|
medium
|
messy/oxidize
|
fair/good
|
medium
|
70%
|
4
|
good
|
$5-$6/gal
|
Mineral Oil
|
low
|
good
|
medium or worse
|
good/stable
|
fair/good
|
difficult
|
50%
|
7
|
excellent
|
$20-$30/gal
|
Biodiesel*
|
low
|
good
|
low
|
good/stable
|
fair/good
|
medium
|
98%
|
4
|
excellent
|
$4/gal
|
- Use of water or water and soluble oil is not recommended unless necessary under special circumstances
- Water has little or no lubrication properties and allow rusting and corrosion to occur in equipment
- Add rust inhibitor to prevent rusting of equipment
- Disposal by flushing down sanitary sewer
- Vegetable oils tend to oxidize and thicken when cold
- Mineral oil is petroleum-based oils such as Texaco’s Almag, Mobil’s Almo 525, Chevron’s Superla #5, Shell’s Pella 21, and Calub SIOS. These are light commercial cutting oils
- Disposal via Hazardous Material recycling/collection after reclaiming liquid from “slurry” by straining through two layers of suspended paper sacks in buckets (long process) and removing solids to landfill
* I have recently switch to biodiesel for a number of reasons in addition to those above – cleans up easily and best of all the rock dust separates in just a few hours. It requires no filtering and reclamation is about 98%!
- Operating the Saw
- Cutting speeds
- Different rocks have different hardness and require different cutting speeds. Matching the speed to the rock will prevent excessive wear and/or heat (which can cause blade warping).
There are two ways to vary cutting speeds. The first way to determine the cutting speed is to start with the speed of the blade itself. This requires matching the drive/motor pulley (the one on the motor) and the arbor or equipment pulley.
- Pulley measurements listed in millimeters (mm) or inches (in). Driven equipment speed in Revolutions Per Minute (RPM). Base on motor speed of 1725 RPM
Dia. Motor Pulley (mm/in)
|
Dia. Arbor Pulley
|
|
|
|
|
|
|
|
|
|
|
|
32 (1.25)
|
38 (1.5)
|
46
(1.75)
|
51 (2)
|
58 (2.25)
|
64 (2.5)
|
76 (3)
|
102 (4)
|
127 (5)
|
165 (6.5)
|
203 (8)
|
254 (10)
|
32(1.25)
|
1725
|
1435
|
1230
|
1075
|
950
|
850
|
715
|
540
|
430
|
330
|
265
|
215
|
38(1.5)
|
2075
|
1725
|
1475
|
1290
|
1140
|
1030
|
850
|
645
|
515
|
395
|
320
|
265
|
45(1.75)
|
2400
|
2000
|
1725
|
1500
|
1340
|
1200
|
1000
|
750
|
600
|
460
|
375
|
315
|
51(2.0)
|
2775
|
2290
|
1970
|
1725
|
1530
|
1375
|
1145
|
850
|
685
|
530
|
430
|
345
|
58(2.25)
|
3100
|
2580
|
2200
|
1930
|
1725
|
1550
|
1290
|
965
|
775
|
595
|
485
|
385
|
64(2.5)
|
3450
|
2870
|
2460
|
2150
|
1900
|
1725
|
1435
|
1075
|
850
|
660
|
540
|
430
|
76(3.0)
|
4140
|
3450
|
2950
|
2580
|
2290
|
2070
|
1725
|
1290
|
1070
|
800
|
615
|
515
|
102(4.0)
|
5500
|
4575
|
3950
|
3450
|
3060
|
2775
|
2295
|
1725
|
1375
|
1060
|
860
|
700
|
127(5.0)
|
6850
|
5750
|
4920
|
4300
|
3825
|
3450
|
2865
|
2150
|
1725
|
1325
|
1075
|
860
|
165(6.5)
|
8950
|
7475
|
6400
|
5600
|
4975
|
4480
|
3730
|
2790
|
2240
|
1725
|
1400
|
1120
|
203(8.0)
|
|
9200
|
7670
|
6900
|
6125
|
5520
|
4600
|
3450
|
2750
|
2120
|
1725
|
1375
|
254(10.0)
|
|
|
9850
|
8620
|
7670
|
6900
|
5750
|
4300
|
3450
|
2650
|
2150
|
1725
|
302(12.0)
|
|
|
|
|
9200
|
8280
|
6900
|
5160
|
4130
|
3180
|
2580
|
2075
|
381(15.0)
|
|
|
|
|
|
|
8635
|
6470
|
5170
|
3970
|
3230
|
2580
|
- The second way to vary cutting speed is to control the speed of the carriage. Controlling carriage speed varies with the brand/type of slab saw but a good ‘rule of thumb’ is to cut slowly.
- Rates for common knappable rock – in inches (work in progress)
Type of Rock
|
Relative Hardness
|
Feed Rate (inches/hour) Varies w/ thickness of rock & stone hardness
|
Obsidian
|
Medium Soft
|
|
Flint - English
|
Hard
|
|
Flint - Texas
|
Hard
|
|
Flint - Flintridge
|
|
|
Jasper
|
|
|
Agate
|
Hard
|
|
Chalcedony
|
|
|
Coral
|
|
|
Chert
|
|
|
Agatized wood
|
|
|
Opalized Wood
|
Soft
|
|
Silicified Wood
|
|
|
Porcelainite
|
|
|
More…….
|
|
|
- Cutting/slab thicknesses
- Slab thickness can be either a personal preference or based on aspect ratio, i.e., thickness to width. Most knappers work slabs between approximately ¼” and ½” (sometimes more) depending on size of the slab, desired size of arrowhead/blade and whether the technique used is percussion or pressure flaking.
- Jim Miller’s thickness recommendations
- For Percussion : Best if the slab is 3/8” thick or thicker
- For pressure: Best if the slab is about 1/4” thick
- Length to Width ratio should be less than 2.5L:1W. If the ratio is larger than this (meaning a long slab relative to width), likely the slab will break in two when attempting to flake an edge all the way around by upstairs/downstairs methods. The exception is for FOG knapping, when almost any ratio can be used.
Cutting orientation
- Cutting orientation refers to cutting a rock to get the most color, character or clarity out of a given slab. A good example is Rainbow obsidian which has bands of color running through it. Two common recommendation are:
- Cut parallel to the band so that the convex shape (lenticular shape) of the point or blade will reveal the layers of color
- Cut at a 10° or 15° bias – same reason as above
- Petrified (opalized/agatize) wood – parallel to grain or slightly offset.
- Securing rock in vice
- Securing a rock in the vice can be as easy as just tightening the vice on the rock. Most vices have relatively soft pads, rubber or plywood that allows the vice faces to grip the rock. Sometimes shims or wedges can be used to help secure them as well (Please note: A large rock that breaks loose or comes apart while sawing can bend or ruin your expensive blade. Wiggle your rock before sawing to assure stability).
- For round rock such as Thunder Eggs or Geodes, a special rock clamp can be used:
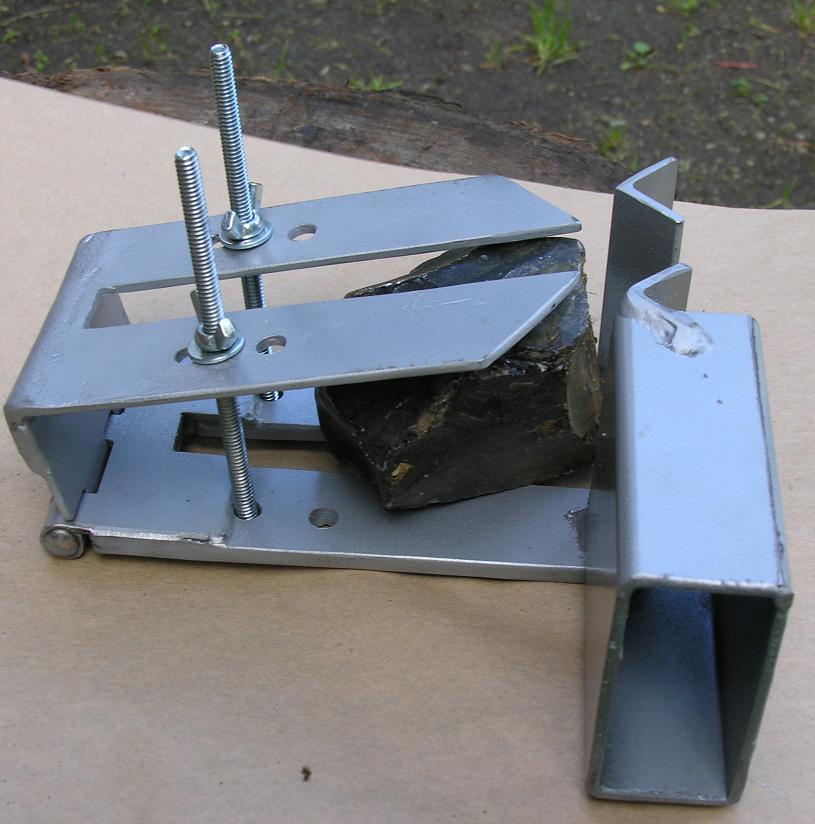
- A slab grabber to mount a piece of rock in the saw vise. These are great after making an initial cut through a rock using one of your clamps.
- In general, a diamond saw blades can cut rock as thick as the clamp and size of the arbor will allow. As an example, a 20” saw blade may only cut rocks up to 8”-9” thick unless a way is found to avoid hitting the arbor, the saw blade washer/clamp, or the rock saw case. Note: You should not attempt to use a smaller saw blade washer/clamp in hopes of being able to feed larger rock with less interference. These large washers are usually sized to minimize blade warping or “dishing.”
- Below are photos of a home-crafted clamp made of strong oak wood and a long bolt that, if carefully used, may allow rock fitted to your saw case size to feed in a saw so as to avoid interfering with the arbor, resulting in cuts of blanks (for example) up to 19-1/2” long in a saw with a 20” diamond saw blade, etc. This must be carefully done and its feasibility will vary greatly from saw to saw because of saw case dimensions, clamp size and grip strength, etc. Not every saw or every person should attempt this as the risks of injury to the saw and/or person increase with the complexity and execution.
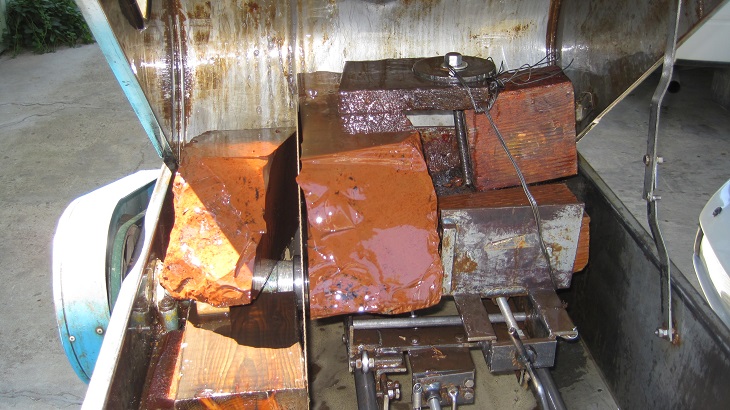
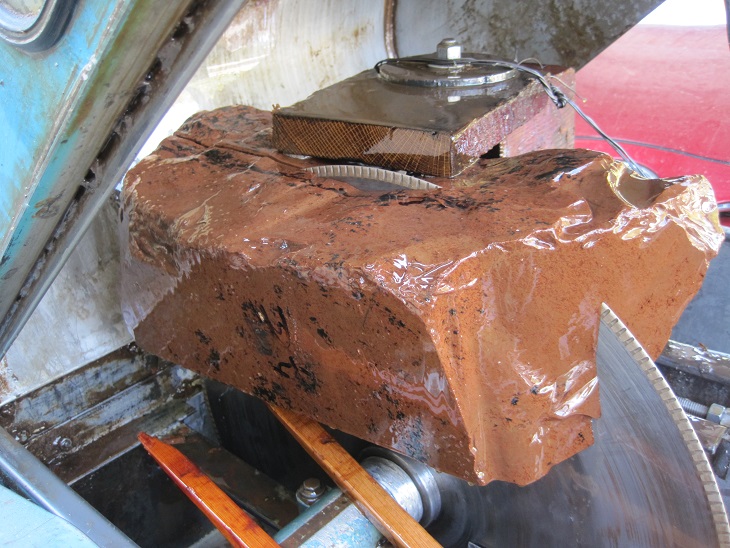
|